Every year, “slips and trips” are costing Australian businesses approximately $48 billion – from mostly preventable workplace accidents. Stopping these kinds of incidents should be a priority for every company, as they are the second leading cause of injuries involving time off. Every year, employees miss an average of 13 days off work from breaks, sprains, strains and tears as a result of tripping.
How safe are your workplace stairs?
It’s easy to slip, trip or fall – anywhere – for any number of reasons. But one of the most accident-prone areas of the workplace is stairs. To ensure that your employees are safe (and not sitting on the couch at home with a sprained ankle) is to first establish a risk assessment plan, followed by careful implementation of simple, practical risk minimisation strategies.
Risk Assessment
At a very basic level, businesses should undertake a “walking surface checklist” being certain to include any stairs. These checklists are available online and will very quickly enable you to see where there are potential tripping risks. Risk assessments should be carried out regularly – at a minimum, once per year. Take particular care to ensure that any metal staircases leading to mezzanines or upper levels are constructed to Australian safety standards. At Advantage Industries, we take pride in ensuring that all our metal staircases are built to code.
Stair Treads and Stairnosing
To reduce the potential for accidents on staircases, stair treads should be constructed from suitable non-slip materials. Stair treads need to be the right depth so booted feet don’t slip off the tread – if a step is too narrow, people will inevitably trip. The front edge of the steps should also have a lighter coloured (yellow) strip called “stair nosing” which improves visibility and traction.
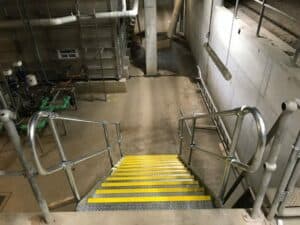
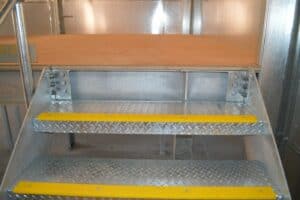
What about Handrails?
Handrails must be constructed from material of the correct diameter, so they are easy to grasp. Employees should be encouraged to use the handrails even when carrying something. All the metal staircases available from Advantage Industries have the option to include sturdy, code-compliant handrails to help keep your employees safely on their feet.
Keep things clean and dry…
…and tidy! There’s nothing so likely to cause an accident on staircases as one that is allowed to become another storage area! Staircases are for walking up and down – not for storing Jack’s lunchbox and Stan’s extra tools! Insist that staircases are always clean, dry and free from obstacles.
Correct Floor Markings
Ensure that floors are clearly marked to show walkways and hazardous areas using reflective safety tape. In addition, tactiles can be used at the top and bottom of stairs to indicate the change of level. Non-skid tape can also be used to improve traction in areas that may be slippery.
And use warning signs too
Warning signs should be used to visually inform workers about potential slip, trip and fall hazards. Every workplace should have “Wet Floor” signs on hand to indicate wet areas, equipment that is leaking or if moisture is being tracked in from outside. Other warning signs such as “Uneven Floors” or “Watch Your Step” can be used to tell people to be careful when approaching hazardous areas. Where staircases could potentially be dangerous, ensure that proper signage is installed to keep workers informed, for example – low headspace can be a problem to tall people.
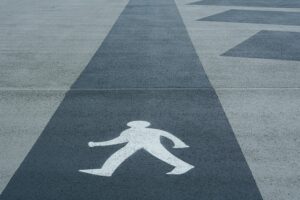
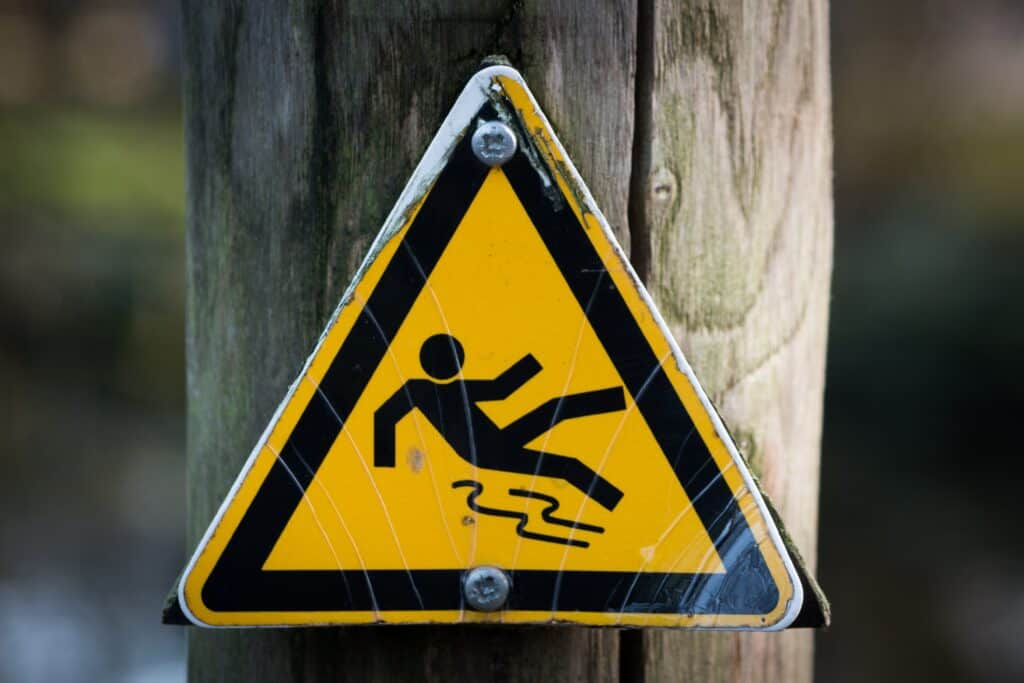
Proper Lighting is Important
When walking through your “hazard” checklist, ensure that your staircases are adequately lit. Nothing is more conducive to tripping accidents than people not being able to see where they are going! Having well-lit stairwells and staircases will help prevent a lot of unnecessary falls. Remind workers to turn on the lights before entering a dark area (or better still – install motion-sensor lights) and be sure to replace light globes that have blown.
Correct Footwear
Workplaces and certain industries that require specific footwear as part of a dress code or safety measure should be sure to enforce the policy to help avoid accidents. Even in office environments, shoes with slippery soles should be avoided. Encourage all your employees to wear correct footwear that provide sufficient traction to avoid slipping, tripping or falling. In particular, should your work environment have stairs, it is imperative that workers wear proper safety footwear with non-slip soles.
Improper use of ladders
Need we even mention this? Improper use of ladders is one of the leading causes of injury in the workplace. Under OHSH laws, the use of ladders for routine operational use is not allowed and workers are not permitted to carry items up and down ladders. Stairs must be installed and at Advantage Industries, we have solutions for most situations!
Repair or replace?
Are your staircases a little – well – 1950’s? Been a while since they were checked for safety? Metal and timber staircases should last a long time, but if your workplace uses chemicals or water regularly, your staircase could become worn and unsafe. It could be time to have a full safety check and replace those old timber stairs that were installed by the previous owner’s grandfather! Doesn’t matter that they look like they should be heritage listed – if they are unsafe, then the potential for slips, trips and falls increases exponentially. A solid, structurally sound metal staircase from Advantage Industries is well worth the cost and is surprisingly affordable. Replace – or at the very least – repair – your stairs BEFORE they cost you money!
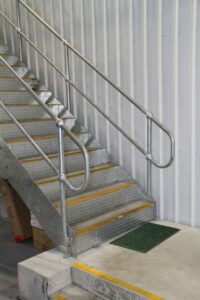
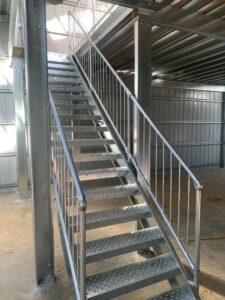
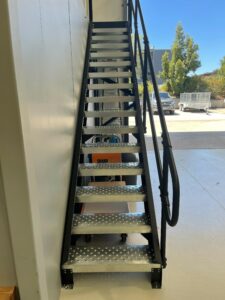
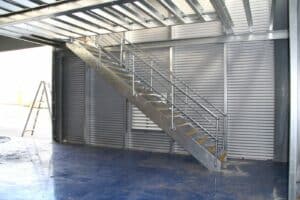
The causes of slips, trips, and falls in the workplace are many. However, most of these accidents can be avoided by taking steps to ensure worker safety. Preventing slips and falls in the workplace not only keeps employees safe but also saves companies the expense of paying for costly injuries. Preventing injury makes more than sense – it makes cents too!
To discuss your staircase options, get in touch with our team today.